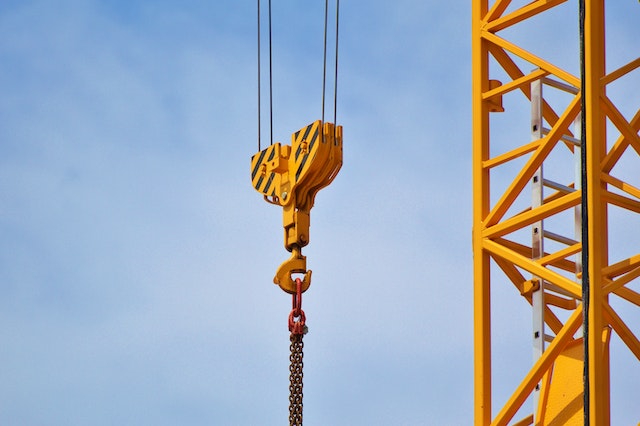
Modern industries rely heavily on high-tech cranes to improve productivity, so it’s vital that employees learn about these devices so they can operate them safely and responsibly.
Manufacturers customise cranes to meet specific conditions. For instance, food industry operations demand lifting equipment that adheres to stringent sanitary standards, while semiconductor production necessitates an enclosed environment.
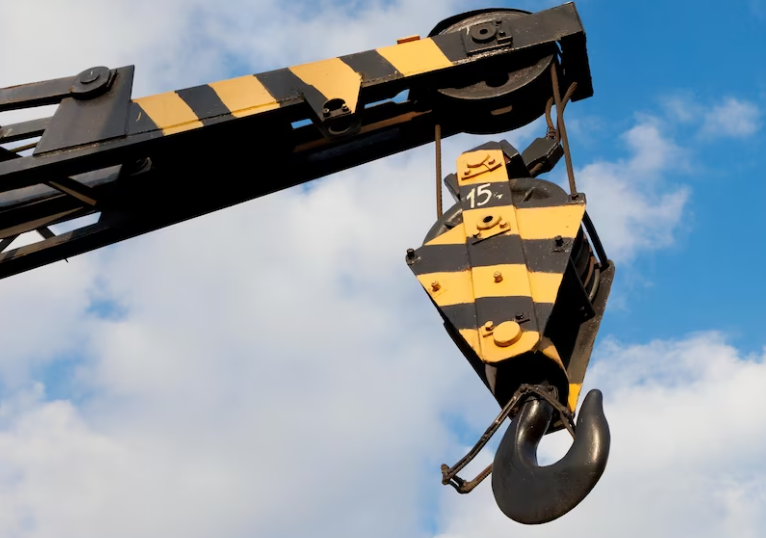
Lifting Capacity
There are numerous styles of cranes, each of which has unique traits that determine its performance. Most models share common components like hooks, hoists, runway bridges, and trolley systems.
Manufacturers determine the capacity of cranes based on their configuration and structural constraints, with load charts representing this information and range diagrams showing their full scope.
If your operation will change in the near future, upgrading the capacity of your crane may be beneficial and much cheaper than purchasing an entirely new unit. But to make sure that you get one suitable for your production requirements and load requirements, make sure your provider provides assistance during this process.
Safety
Overhead cranes are complex machines that require expert knowledge to operate safely. Any errors made while managing an overhead crane could lead to severe injuries and accidents.
Accidents involving overhead cranes often result from improper maintenance or inspection, overloading of equipment, and disregard for safety rules. Such errors can cost businesses an exorbitant sum in terms of repairs or replacement expenses for damaged equipment.
Workers should be properly trained and informed of the standard hand signals used for crane operations. Furthermore, they must understand load dynamics and lifting capacities at various configurations as well as inspect the area where the crane will operate for obstructions such as power lines. All cranes must also come equipped with primary upper limit devices and secondary brakes to protect workers during operations.
Maintenance
Maintenance on cranes is part of working in an industrial setting. Regular inspections should be performed to detect small issues before they turn into major ones and save on costly repairs.
An effective crane maintenance routine begins by conducting an initial safety inspection to make sure there is nothing nearby that could get caught or damaged by the machine. Next, an operator must inspect all powered systems, including making sure that power buttons on pendants don’t get sticky and hoist hooks rise as intended.
Finally, inspection includes inspecting all lubrication points for cleaning and oil lubrication as well as checking each agency brake’s institutional part for cleanliness and lubrication needs. In addition to replacing broken or worn parts if necessary.
Speed
Employing an overhead crane allows large products to be moved more easily through a facility or loaded onto trucks for transportation, improving workflow efficiency in manufacturing, mills, warehouses, and anywhere where heavy materials need lifting, manoeuvring, and positioning.
In choosing the appropriate crane for your business, there are various factors to keep in mind, including lifting capacity, span, lifting height, and running speed. Aicrane professionals take these technical data points into account and match you up with a system tailored specifically to your requirements—plus, they can even assist with its installation!
Efficiency
Overhead cranes can work up to 2-3 times faster than workers or tow motors when lifting and moving materials, providing manufacturers, mills, and warehouses the opportunity to streamline processes and procedures at their facilities.
Crane controls give their operator complete command over the load at all times, from basic start/stop buttons to joysticks and tablets that allow the programming of complex movements and motions.
Brakes on both the hoist and bridge are another crucial aspect that contributes to efficient performance. Most modern cranes utilise an electric motor system that automatically adjusts and compensates for wear on braking linings or composite journal bearings to minimise maintenance requirements and downtime.
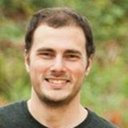
Garrick is a sports writer specializing in horse racing. He focuses on delivering race analyses, jockey and trainer insights, and coverage of major events, aiming to provide readers with up-to-date information and in-depth perspectives on the racing world.